Case Study: How Bari Consulting Rescued a Fleet in Crisis
Understanding the Crisis
When a major logistics company faced a sudden crisis with its fleet, it turned to Bari Consulting for a solution. The company had been experiencing significant delays in deliveries due to unexpected vehicle breakdowns. This not only affected their operational efficiency but also threatened their reputation with clients. The situation was dire, and immediate intervention was necessary to prevent further damage.
The root of the problem lay in the maintenance processes of the fleet. The company had been relying on outdated methods and tools, leading to unscheduled downtimes and increased repair costs. Employees were overwhelmed, and morale was dropping as stress levels soared.

Bari Consulting's Strategic Approach
Bari Consulting conducted a comprehensive analysis of the logistics company's operations. They identified key areas that required urgent attention and developed a tailored strategy to address these issues. The plan focused on three main components:
- Implementing Predictive Maintenance: By integrating advanced diagnostic tools, Bari Consulting enabled the company to predict potential failures before they occurred.
- Streamlining Operations: Optimizing routes and schedules to enhance efficiency and reduce stress on the fleet.
- Training and Development: Providing ongoing training to staff to equip them with the knowledge and skills needed to maintain the fleet effectively.
This strategic approach promised not only to resolve current issues but also to set a foundation for sustainable operations in the future.
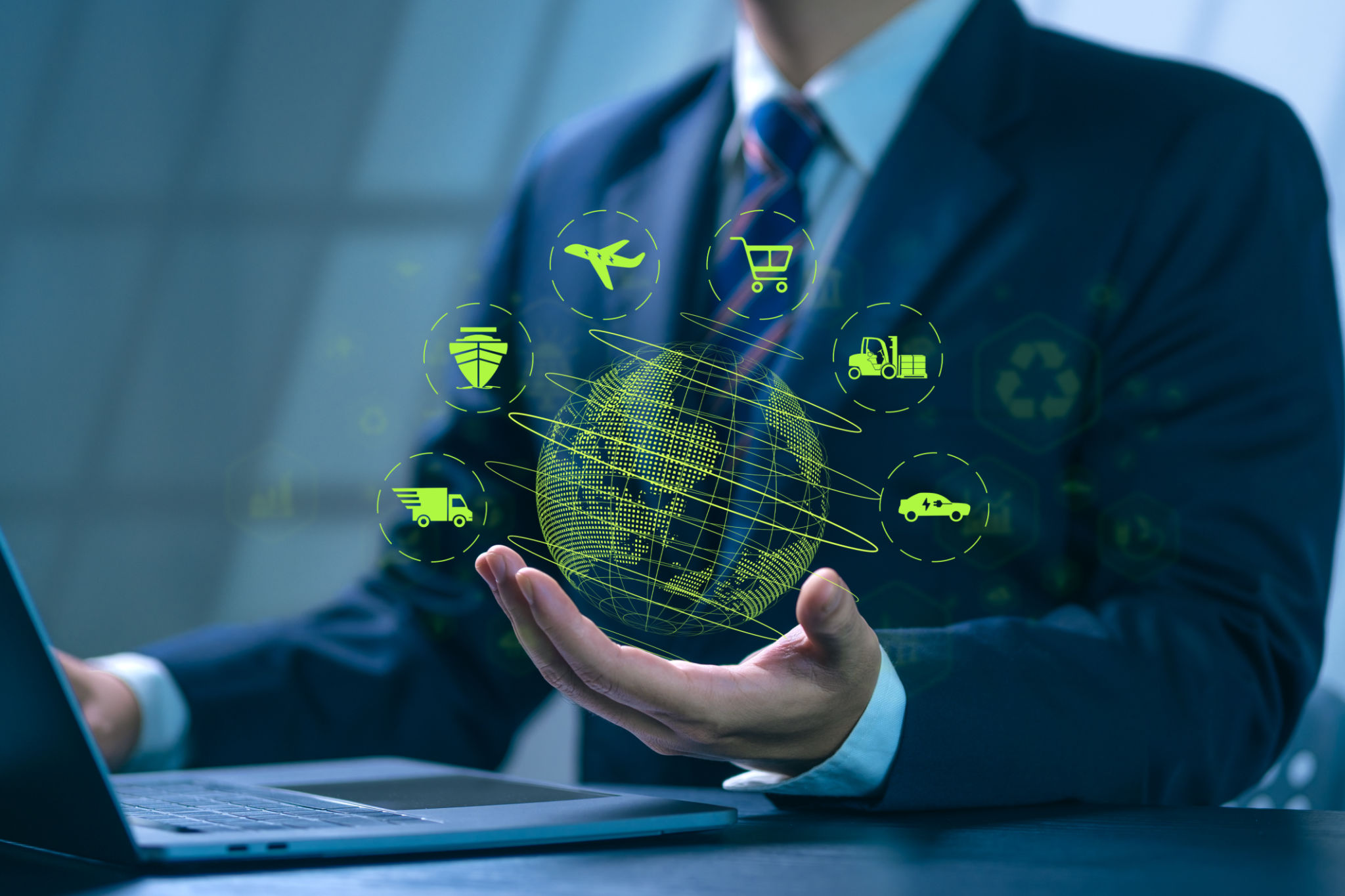
The Implementation Process
The implementation of Bari Consulting's strategy began with the installation of state-of-the-art diagnostic equipment across the entire fleet. This technology provided real-time data on vehicle performance, allowing for timely interventions. Predictive maintenance schedules were established, significantly reducing the frequency of breakdowns.
Next, the consulting team worked closely with the logistics company's management to optimize delivery routes. By leveraging data analytics, they minimized fuel consumption and travel time, ultimately enhancing customer satisfaction. Meanwhile, staff training sessions were conducted regularly, ensuring that employees were well-versed in new maintenance protocols.
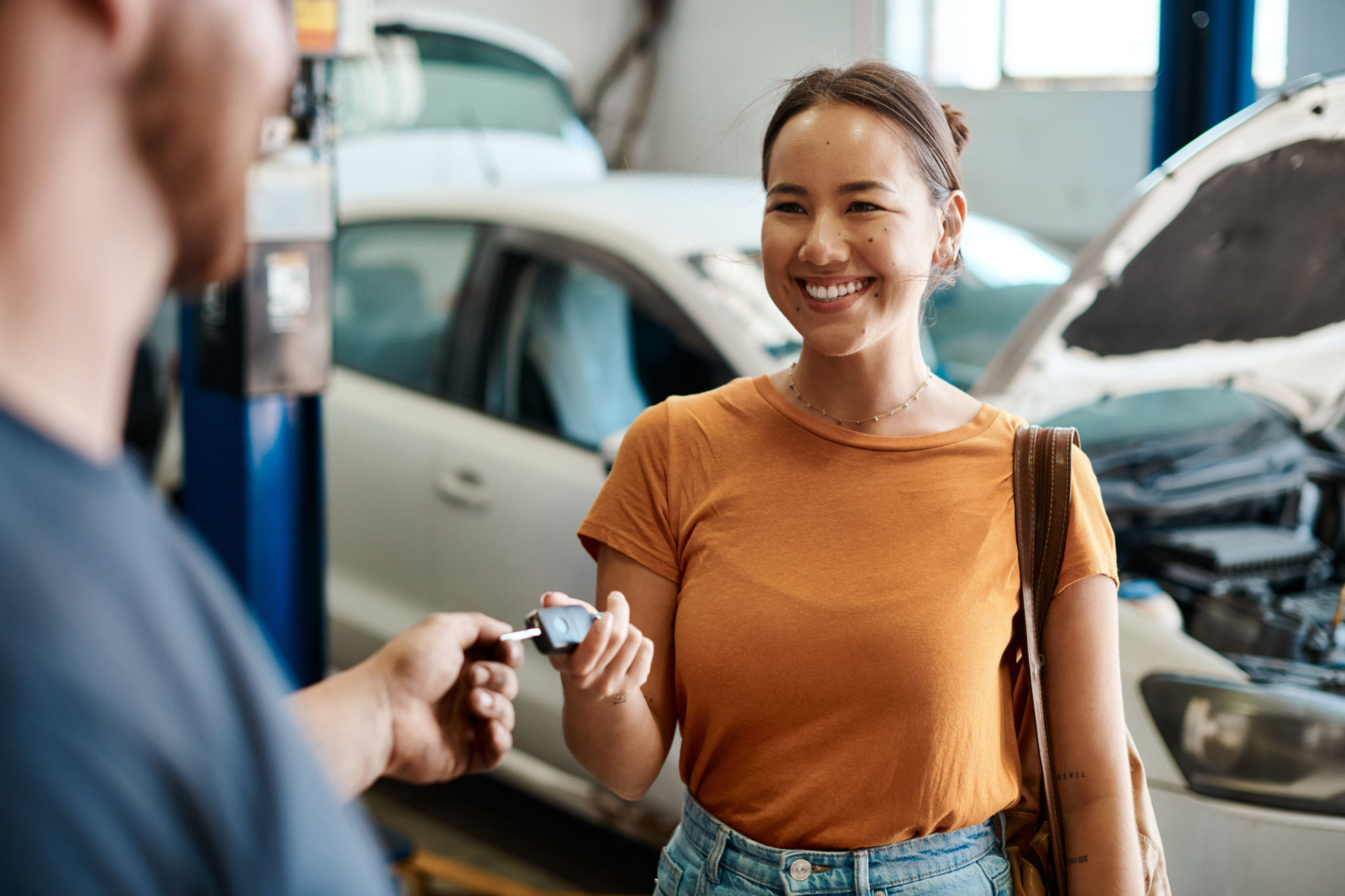
Measuring Success
The results of Bari Consulting's intervention were profound. Within just a few months, the logistics company experienced a dramatic reduction in vehicle breakdowns. Deliveries were back on schedule, and customer complaints dropped significantly. The fleet's overall performance improved, leading to increased client trust and new business opportunities.
Moreover, the cost savings achieved through optimized operations and reduced repairs allowed the company to invest in further innovations. Employees reported higher job satisfaction as they were empowered with the tools and knowledge to perform their roles effectively.
Lessons Learned
This case study highlights the importance of adopting modern maintenance practices and leveraging technology in fleet management. Bari Consulting demonstrated that a proactive approach could transform a crisis into an opportunity for growth and improvement. By focusing on predictive maintenance, operational efficiency, and staff development, businesses can safeguard their operations against future challenges.
The success story of this logistics company serves as a testament to the power of strategic consulting and innovative solutions in overcoming operational hurdles.
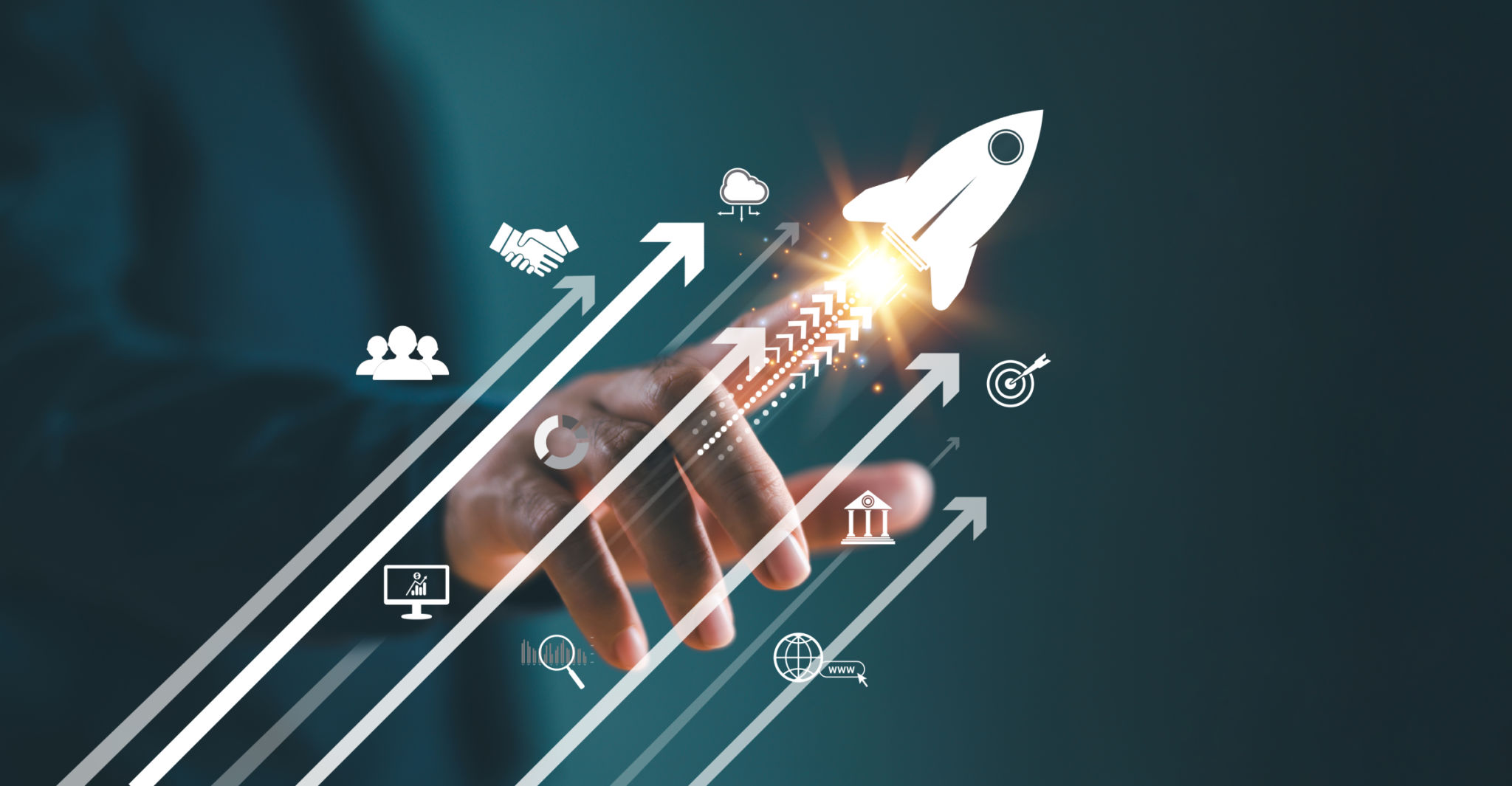